The copper roofing pans are turned up on the vertical wall to form a base flashing extending at least 9 up the wall where they are cleated. Fasten the folded sides of the gable with stitch screws.

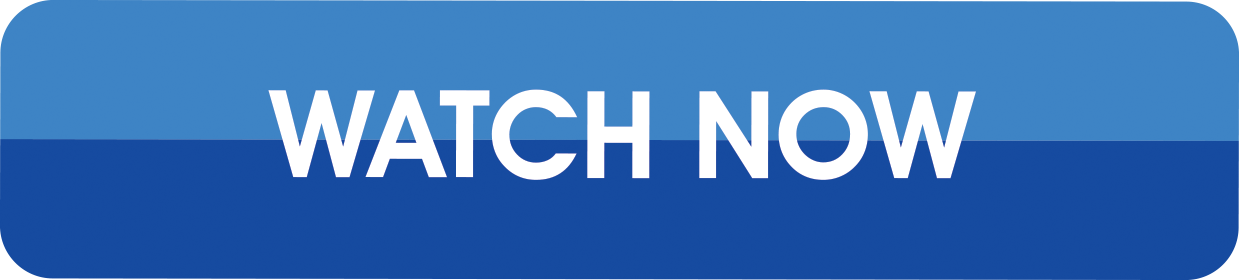
The flashing shall be a minimum of 4 inches (102 mm) high and 4 inches (102 mm) wide.


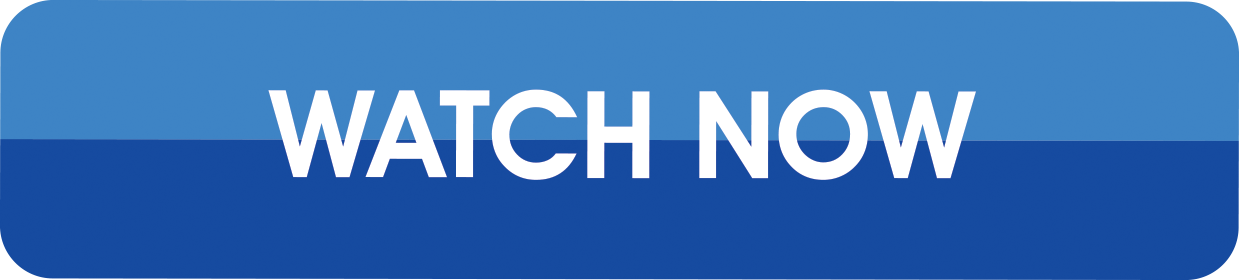
End wall flashing detail. • through wall flashing at the base of the walls should be located 2” or 3” (50 or 75 mm) above finished grade. Flashings are restricted in length in the same manner as are roof and wall cladding sheets and are subject to the same requirements and expansion provisions. To allow movement due to thermal expansion, at one end of every
You can also use pop rivets to fasten the flashing. Install metal roof endwall trim at the sidewall. Beyond end of lintel cavity insulation not shown for clarity of detail sealant note:
• do not seal housewrap or building paper to step flashing. This detail can be used for both standing and batten seam roofs. The end wall flashing provides protection where a roof intersects with a vertical wall.
At the end of the vertical sidewall the step flashing shall be turned out in a manner that directs water. Flashing edges beneath cladding normally only require nominal attachment to battens. Structural elements may vary, and are shown for illustration only.
Fasteners close to folded edges generally cause the least distortion. • any cavity space below the flashing at the wall base should be completely filled with mortar. The flashing is continuous and projects beyond the face on both sides of the wall.
Prefabricated flashing end dam carry flashing ½” min. From any corner or end of wall. Pitched copper roof parallel to wall.
End dams are constructed by cutting and folding the flashing material. International masonry institute team masonry detailing. The “down” direction harnesses the force of gravity and the “out” direction gets the water away from the building enclosure assemblies, openings, components and materials.
In the northern climates, the brickwork should be at least 6” (150 mm) above grade. As a result, parapet walls can crack, heave, or bow. Step by step endwall flashing installation instructions on a metal roof.
Gibraltar end wall flashing can be used with most metal roofing profiles. Above a lower roof where it abuts the wall; Flashing single wythe walls at the ends of bar joists which utilize wall pockets for bearing is shown in figures 8 and 8a.
Critical wall flashing details at decks and porches. Where flashing is metal, the metal shall be corrosion resistant with a thickness if not less than 0.019 inch (26. Joints are soldered or sealed (see figure 2).
This color matched flashing also provides a professional finishing touch to your roof. Plates and fasteners get installed at the seam—vertically up the wall at 12 in. It is critical to protect against leaks and water buildup at deck ledgers, since decay in this part of a building can lead to structural failure of the deck.
End dams should be constructed wherever flashings terminate within a wall to prevent water from simply flowing off the side of the flashing within the masonry wall rather than being directed to weeps where it can flow out of the wall. In all cases, make sure to detail the flashing membrane so that it sheds water. It should tuck under the sheathing wrap above and over the flashing below.
If installed along the foundation, the membrane should cover the joint where the sill meets the foundation. Gravity is the driving force behind drainage. A 75 mm minimum wall cladding cover over the upstand a 35 mm minimum gap.
On center and a minimum of 10 ft. The dowel securing the masonry coping is fully covered by a copper cap soldered to the flashing. Used in conjunction with closure strips or butyl tape, it reliably protects against water infiltration.
Copper flashing, held by a receiver at the top, is locked into a locking strip soldered to the base flashing.

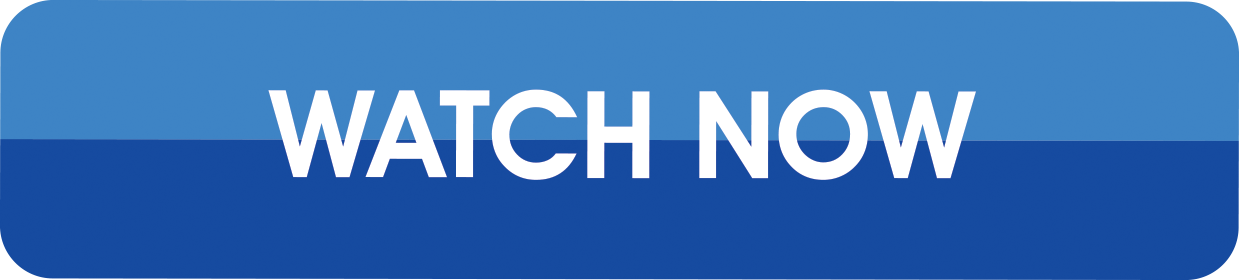

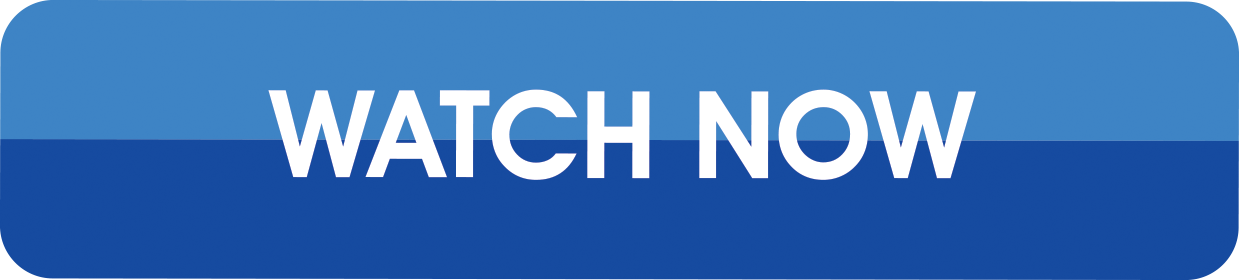

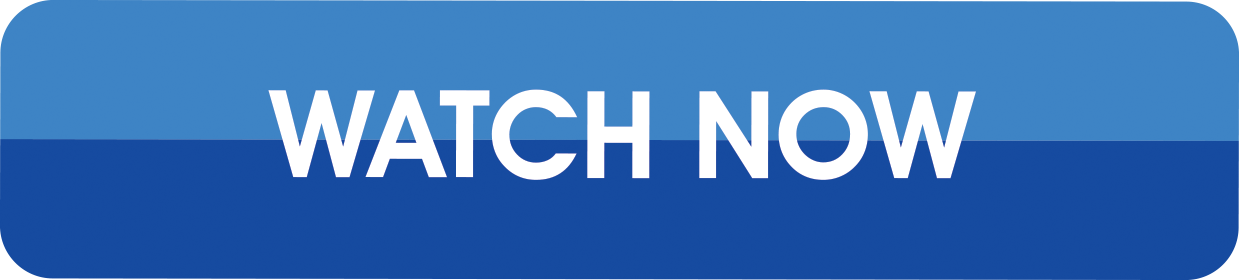
0 komentar:
Posting Komentar